Hot dip galvanized stud bolts are an essential component in various industrial and construction applications, offering enhanced corrosion resistance and durability. These bolts are extensively used in environments where exposure to moisture, chemicals, or harsh weather conditions can lead to corrosion and deterioration of standard fasteners. In this article, we will explore the process of hot dip galvanizing, the advantages of using galvanized stud bolts, and their common applications.
The Hot Dip Galvanizing Process
Hot dip galvanizing involves coating steel or iron bolts with a layer of zinc to protect them from corrosion. The process includes several steps:
- Cleaning: The bolts are cleaned to remove any dirt, oil, or rust. This is typically done through a series of chemical baths, including degreasing, pickling (using an acid solution to remove rust), and fluxing (applying a flux solution to prevent oxidation before galvanizing).
- Galvanizing: The cleaned bolts are submerged in a bath of molten zinc at a temperature of around 450°C (842°F). The zinc reacts with the steel to form a series of zinc-iron alloy layers, creating a robust and durable coating.
- Cooling: After galvanizing, the bolts are cooled in a quenching tank, which solidifies the zinc coating and enhances its adhesion to the steel.
- Inspection: The galvanized bolts are inspected to ensure the coating is uniform and meets the required thickness standards.
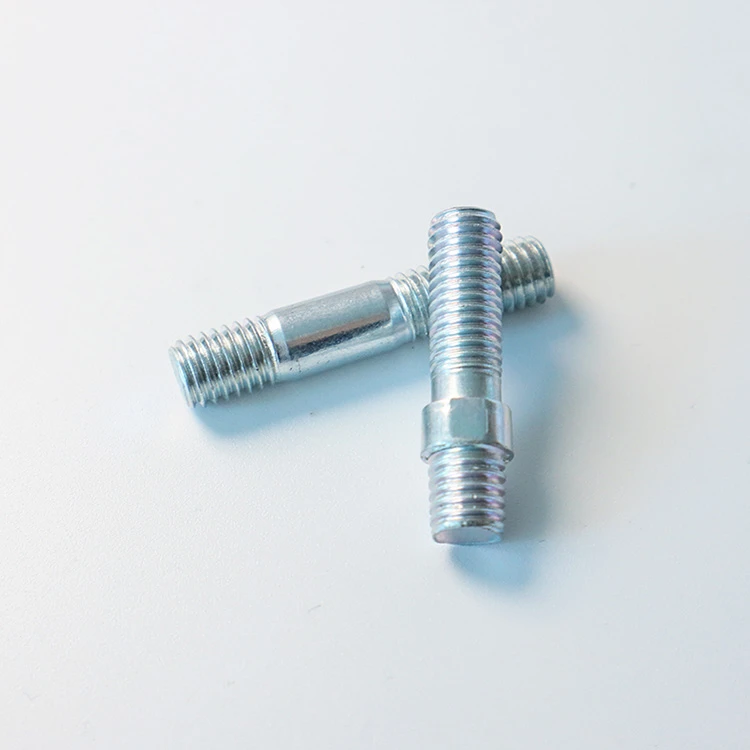
Advantages of Hot Dip Galvanized Stud Bolts
The hot dip galvanizing process offers several benefits, making these stud bolts an ideal choice for many applications:
- Corrosion Resistance: The zinc coating provides a barrier that protects the underlying steel from moisture and oxygen, significantly reducing the risk of rust and corrosion.
- Durability: The metallurgical bond between zinc and steel creates a tough coating that can withstand mechanical damage and harsh environmental conditions.
- Long Service Life: Hot dip galvanized bolts have a long lifespan, often lasting several decades without significant maintenance, even in aggressive environments.
- Cost-Effective: Despite the initial cost of galvanizing, the extended service life and reduced maintenance requirements make hot dip galvanized bolts a cost-effective solution in the long run.
- Sacrificial Protection: Zinc acts as a sacrificial anode, meaning that even if the coating is damaged, the exposed steel is still protected as the zinc will corrode first.
Applications
Hot dip galvanized stud bolts are used across a wide range of industries due to their exceptional performance and reliability:
- Construction: In building structures, bridges, and other infrastructure projects, these bolts ensure long-term stability and safety by resisting corrosion in outdoor environments.
- Maritime and Offshore: In shipbuilding, docks, and offshore platforms, galvanized bolts withstand the corrosive effects of seawater and humid conditions.
- Energy Sector: In power plants, wind turbines, and solar installations, hot dip galvanized bolts provide reliable fastening solutions that endure extreme weather and temperature fluctuations.
- Agriculture: In farming equipment and structures like barns and silos, these bolts resist corrosion from exposure to soil, chemicals, and varying weather conditions.
- Automotive and Transportation: In vehicles, railway systems, and road infrastructure, galvanized bolts enhance safety and longevity by resisting rust and wear.
Conclusion
Hot dip galvanized stud bolts are a critical element in ensuring the durability and integrity of various structures and equipment exposed to corrosive environments. By understanding the galvanizing process, recognizing the advantages, and knowing the common applications, engineers and builders can make informed decisions to enhance the longevity and performance of their projects. The reliability and cost-effectiveness of hot dip galvanized bolts make them a preferred choice in many industrial and construction applications, contributing to safer and more resilient infrastructure.